When you see the letters AC/DC, the first image that may emerge in your mind is the world-popular rock band singing “highway to hell,” right? But sorry to disappoint you, our today’s destination is not hell, but acknowledging the difference between AC and DC welding.
Now, when it comes to learning welding, the mountainous stacks of information might seem like a raging avalanche approaching you.
But no worries, we are here to protect you as a great wall between you and the torrent of information. We will make sure that you get only the essential information’s about AC vs Dc welding.
First and foremost, to differentiate two different things, we have to know what they are. With that in mind, let’s start with getting to know what is AC and DC welding and their pros and cons.
Table of Contents
What Is AC Welding?
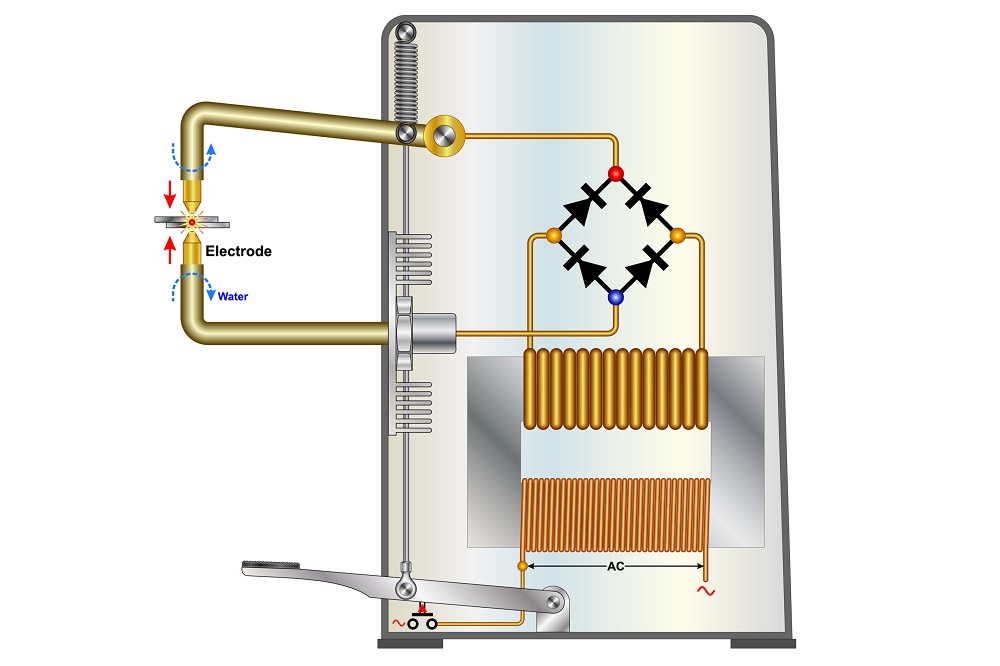
AC or alternating current is the electric current you will find in AC welding. In this process, the current gets alternated between positive and negative. It’s not like those straight wires you see on the electric pillars, but a wavy line you will mostly see in-home wiring.
So, when it comes to AC welders, what they do is pass the current flows without any sort of modifications. We will learn more about AC welding down below. Let’s keep reading.
Why Choose AC Welding?
If AC welding had any major issues, then it would not have survived this long, and that’s common sense, right? AC welding has made a lot of applications easier to operate and repair.
What’s going to impress you the most about AC welding is that you can work on metal that has a magnetic field without any hassle.
If you have ever got to weld metal with a magnetic field, you might be aware that the welding arc may get out of alignment with the electrode. It’s because of the magnetic current in the metal you are welding.
In the welding world, this is known as Arc wandering. And this issue can give you some trouble getting clean and straight welds. The good news is AC welding is not vulnerable to such issues.
Especially when it comes to repairs on machinery that has magnetic fields, AC welding will save your day.
AC welding process is a lot cheaper than DC welding. So, if managing a budget is a problem, it would be wise to get started with AC welding. You won’t have any issues with higher temperatures when you are using this method, so welding material like aluminum is easier now.
When your work involves welding deeper into the material, for instance, shipbuilding industry then, AC welding is a great choice as it’s incredibly powerful and its strong weld is enough to penetrate deep plate metals.
The Downside Of Ac Welding
Let’s get real; you won’t find anything 100% perfect made by humans. Everything has its advantages and disadvantages, just like we humans have good sides and dark sides.
It’s the same when it comes to AC welding. The first issue we cannot help mentioning is that the welding current is always alternating its direction in AC welding.
And when the current changes direction, the machine will go through a moment with no amperage. That will create a lot of swings in the arc of your welder, and that’s what makes it hard to get a clean-cut using AC welding.
Besides that, AC welding also creates far more splatter than DC welding. So, when you are going for vertical welding or overhead welding, it’s not going to be a walk in the park.
Here, we have pointed out the pros and cons of AC welding. In short, to make it clearer and easier for you to understand.
Pros
- AC welder comes with an affordable price tag.
- No worries with arc blow issues.
- Great at aluminum welding.
- Weld materials with magnetic field without any trouble.
Cons
- Dealing with constant fluctuation.
- Not getting the perfectly smooth weld.
- More spatter than DC welding.
What Is DC Welding?
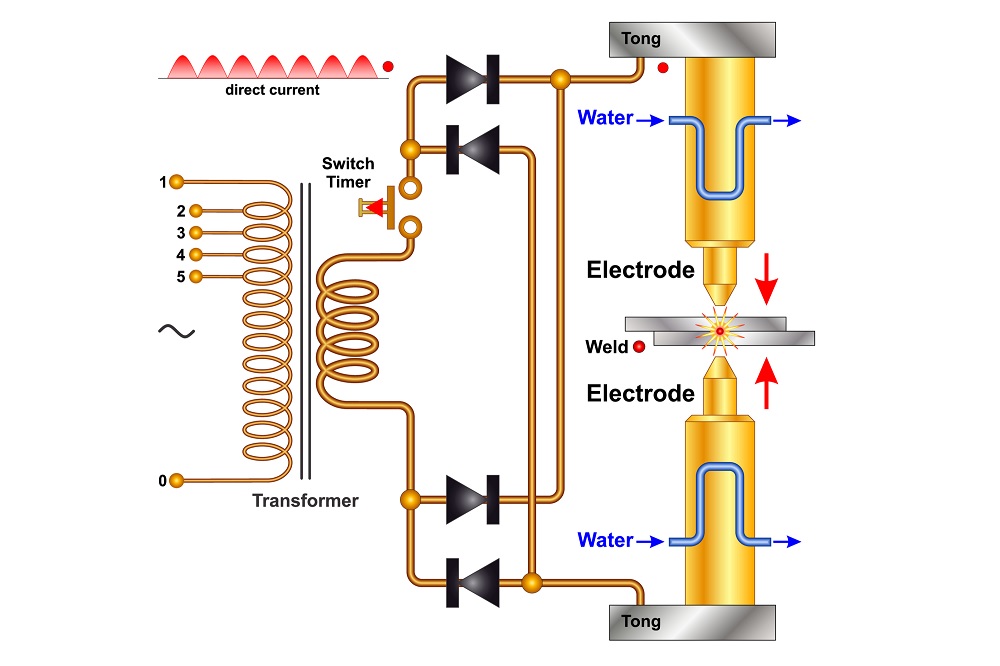
DC means direct current, and the name says it all. In DC welding, the supply of the electrical current is straight as an arrow. It’s not wavy like in AC, it goes in a linear direction. When it comes to DC welding, the current flows are passed to the electrode directly, which plays the role of protagonist to join the two metals.
You see the straight lines of wires in the electric pillars by the road; that’s the DC line. In DC welding, you won’t have to deal with the constant stopping of the arc on each swap of polarity.
Electrode positive and negative current polarities can be used in direct current. The negative polarity of the electrode is also known as Straight Polarity. Most welding tasks are done using straight polarity. It makes the arc a lot hotter than positive polarity, and that melts the electrode faster.
You will be able to get your work done much quicker as it allows you to frame the bead faster. With electrode-positive or also known as reverse polarity, you will get a deeper penetration ability.
So, welding thick material is not rocket science anymore. It’s not as fast as straight polarity, to be honest, but it’s the best solution you have when working with thick materials.
Why Choose DC Welding?
If you are looking for a clean-looking, visually pleasing weld, DC welding is the way to go. You won’t have to deal with much spatter in DC welding. Also, its non-changing polarity and steady control will give you exactly the weld you expected.
DC welding is mostly used where looking visually pleasing matters a lot. For instance, vehicles, furniture, and tools. It’s also very effective in making parts that go through extreme pressure or stress.
It does not have any zero-amperage as you see in AC welding. DC welding is quite easier to control. As it does not produce much spatter like AC welding so, overhead welding is not mission impossible.
The learning process is not that hectic so, it will give you the much-needed confidence and let you learn to weld better and faster. However, it’s still better to get started with AC welding for beginners as it’s cheap and doesn’t involve much technical stuff.
The Downside of DC Welding
Just like AC welding, Dc welding has also got some downsides. The first downside that might turn you off is its sky-high price. You won’t get DC in any electrical grids; therefore, you will have to manage an internal transformer to transform the current from AC to DC.
And managing all those is going to take a toll on your budget. To run DC, you will require 220-volts circuits, so you will need an electrician who is an expert at this. That can drain a lot of bucks out of your pocket.
Another major issue with DC welding is arc blow. When it comes to deal with the magnetic current in your weld metal, it’s going to ruin the alignment of the arc with the electrode resulting in messing up the bead. Because of this reason, most of the welders out there prefer to use AC welding.
You won’t have to deal with such an issue when working with AC welding. Operating DC welding is not a child’s play; it requires high-professional skill and knowledge about welding and electricity.
Down below, we have pointed out the pros and cons of DC welding, in short, to make it clear and easier for you to understand.
Pros
- Gets more well-shaped and smoother weld.
- No worries about the unstable arc.
- Less spatter clean welding.
Cons
- Dealing with magnetic arc blow.
- Quite expensive.
The Key Differences Between AC and DC Welding
To understand the difference between AC and DC welding, here’s a table for you.
AC Welding | DC Welding |
AC welding alternates polarity. | DC welding works with positive or negative polarity. |
Generally used in welding aluminum, thick metals, and magnetized materials. | Welding overhead materials and TIG welding are easier with DC welding. |
Not much powerful and produces heavy spatter. | Its strong, smooth and, produces less spatter. |
No potential for arc blow. | You have to deal with the arc blow issue. |
Comparatively cheaper. | Costs a lot more than AC welding. |
After having a look at the comparison table, we hope now the difference is much clear to you. To understand some more basic welding stuff, please, keep reading.
Is AC Welding Better than DC Welding?
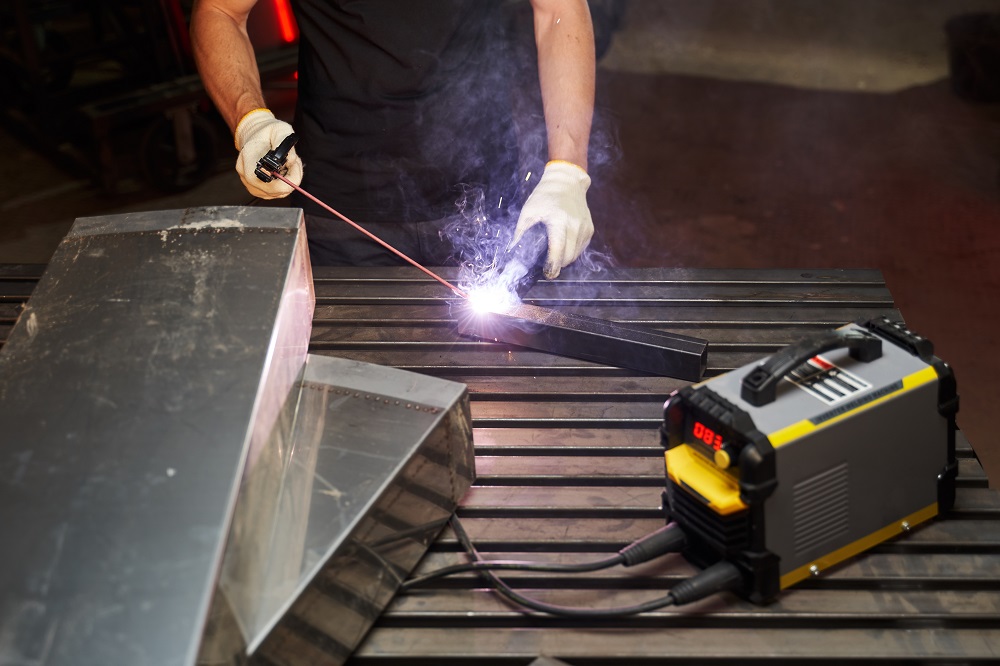
If you have zero experience with welding, then it could be a little bit tricky for you to understand the reality. Still, we will give our best to explain. You know, there’s a saying, “the truth lies in the gray zone rather than black and white.”
So, when it comes down to which is the best welding method, the truth is it entirely depends on your requirements. Let’s have a closer look at different scenarios.
When it Comes to Starters
If you are one of the hobby welders out there, DC welding will offer you great comfort in operating and a clean welding result. But, here’s the sad truth, you cannot afford a DC welding machine by breaking your piggy bank. And this might be a ‘big no’ for many beginners. On the other hand, AC welding is a lot cheaper so, novice welders can afford it easily.
When Welding Weld Thin Metals
Welding thinner metals is a no-brainer with DC welding as it the process is done under lower temperature. You won’t have to deal with any risk of putting a hole through the material when welding.
When Welding Aluminum
AC welding will give you a better result than DC when welding aluminum. It can generate a lot higher temperature, which is essential in welding aluminum. DC welder cannot reach that much of a higher temperature, making it a wrong choice for welding aluminum.
When Welding Overhead Material
DC welding produces less spatter than AC welding. So, you have no issues with overhead welding. AC welding produces a lot of spatters when operating. Therefore it becomes challenging to weld overhead objects using it.
A Quick View on When to Weld with Which
If you have become puzzled after reading loads of information, here’s a quick glimpse at the essential factors about AC and DC welding.
When to Use AC Welding
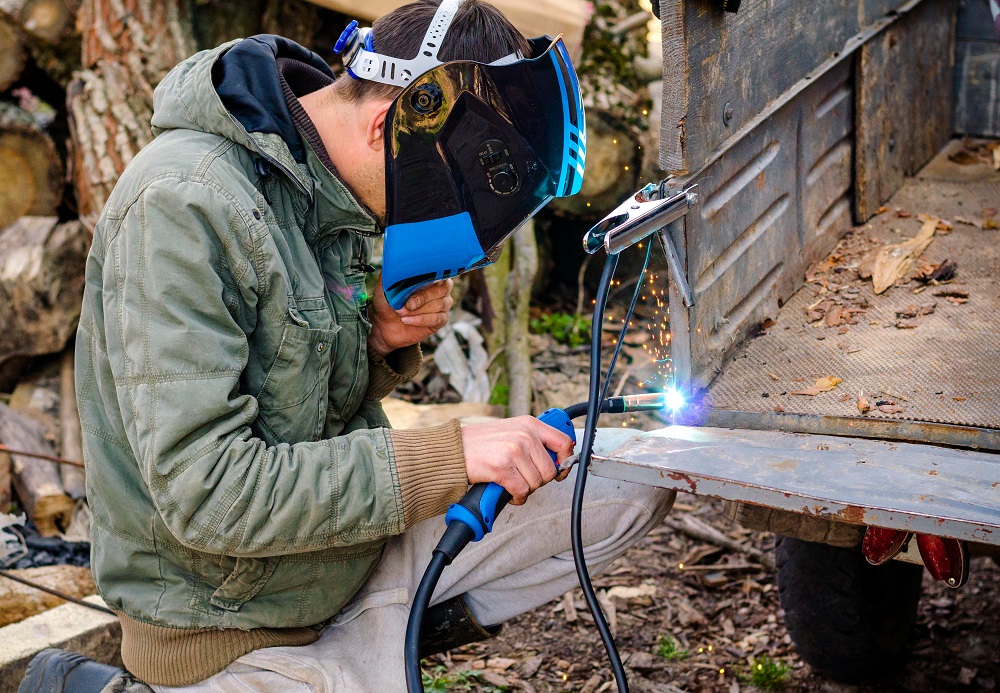
- The look and feel don’t matter much.
- You don’t have a big budget.
- Need to make deep penetration of heavy plate metals.
- When it comes to weld metal that has a magnetized field.
- When welding aluminum.
When to Use DC Welding
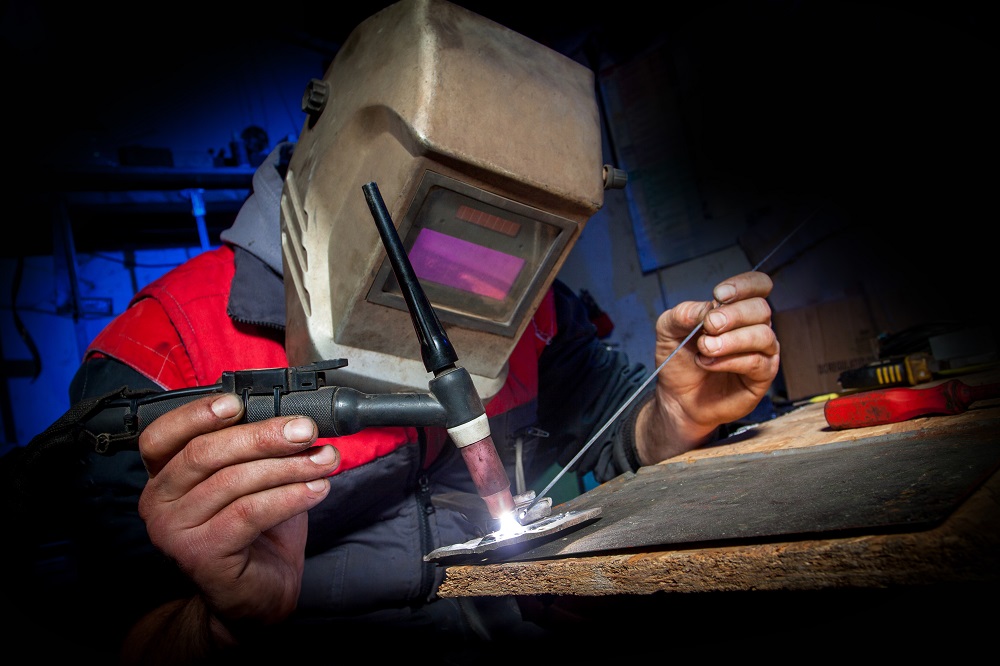
- You need a very clean-looking and aesthetic weld.
- You have no issue with the budget.
- When it comes to weld sheet metal.
- When welding overhead objects.
We hope these bullet points made things a lot easier for you. And now it’s more vivid to you which welding method to use at what circumstance.
Frequently Asked Questions
Q1. What Type of Current MIG Welding Use?
Ans. Most of the MIG welding machines out there runs by DC. However, there are some affordable gas-free models of MIG welders in the market, as well.
Q2. Is it Safe to Use AC Welding?
Ans. If you can install and use the arc welding option following the proper method, you are not supposed to have any severe issues. But if you fail to follow the safety measures, it can cause you serious injuries.
Q3. Are AC Welders Lighter in Weight Than DC?
Ans. Yes, AC welders are a lot lighter than DC welders and, that makes them easier to handle.
Final Verdict
So, AC vs DC welding, the great battle has come to an end. And now we have reached a new height from where we can see, clearly who won the battle. It’s neither AC current nor DC, as both have their highlights and challenges. The welding types rely on the type of your work and skills. For a starter, we have recommended AC welding as it comes with an affordable price tag.
On the other hand, if you have good experience in this field and budget is not an issue then, DC welding is the way to go. We hope, after reading this far, you have no more confusion with AC and DC welding. That will be all for today.
Happy welding!